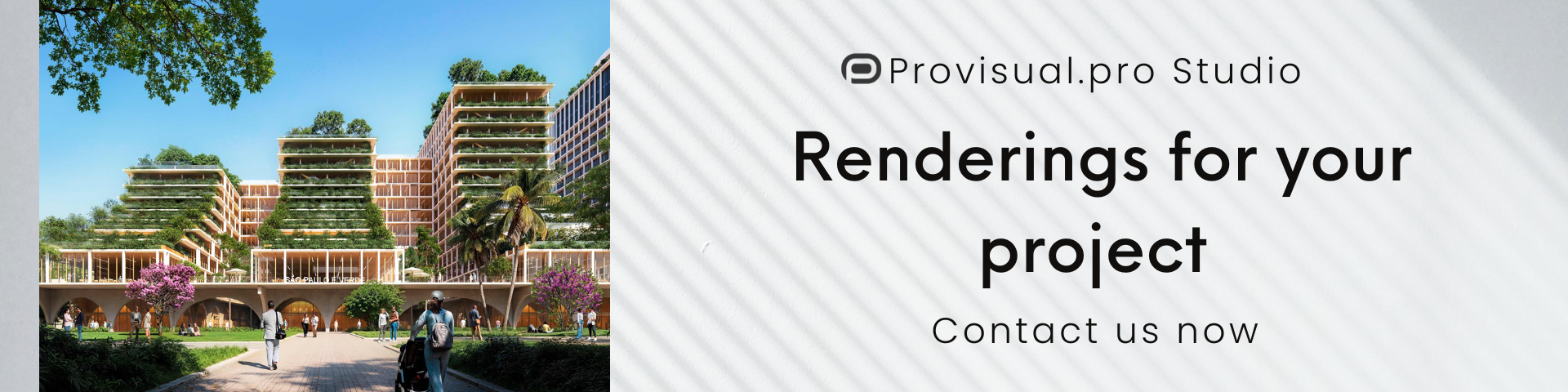
Xerox’s market entry in 3D printing was a muddled and confusing affair. A mention at an investor conference led to us realizing that the company had bought metal dripping startup Vader Systems. So Xerox wasn’t going to be working with inkjet heads or going to do something like Evolve Additive with thermal heads, laser or toner, it wasn’t going to do polymer but instead metal. And in metal, it wasn’t going to try join the binder jet hype train but instead do something new. And that new thing wouldn’t be something that Xerox itself had developed but it was going to be something that they bought. It all felt a tad bit rushed. My initial foray into exploring their metal parts wasn’t promising either, the half centimeter high objects seemed a better fit for Hackaday than Formnext.
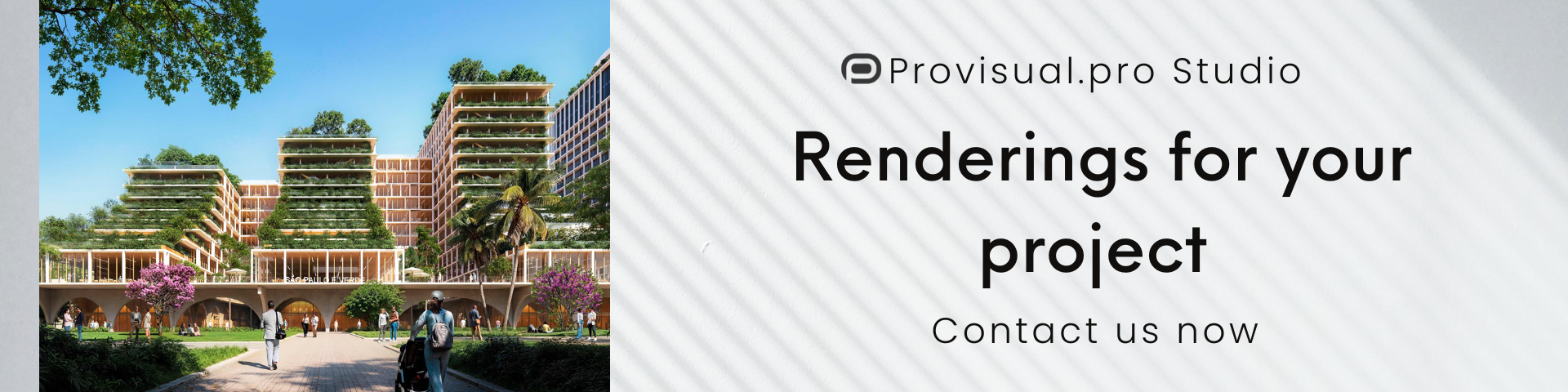
The thing about the Vader technology is by having a technology that uses electromagnetic force to drip molten metal, they have their very own technology stack. Only they use a wire spool that’s melted in a ceramic crucible where the drops are then forced out by electromagnetic force onto a moving build plate. On the one hand, it means that Xerox will have to do all of the heavy lifting itself with little help from universities, customers and other vendors doing research in the space (as is happening with DED, DMLS, EBM). On the other hand, they can develop a completely unique 3D printing technology. By using off the shelf wire and moreover, being able to use a wide range of low cost wire feedstock, they could have a versatile technology that could fill niches that others have not considered. If they could serialize this technology and have many heads drop many droplets or do things such as rare alloys or materials others could not use then this could be very exciting. Currently they can use several steels (316, 718) as well as aluminum.
Xerox’s Kevin Lewis, who currently leads their 3D printing effort, is already excited by the prospects of Xerox’s metal technology. He says that “what made us look at it was that the market time was right..and looking at the patent portfolio kept us going.” The firm has long experience “selling printheads” to the 3D printing industry but it was “Vader systems technology..and that it is a comparatively safe process..with a good cycle time.” that got them interested in the technology. It is notable that the firm thought of production from the get-go. Additionally, Xerox liked that Vader was, “using a low-cost material, aluminum..and had no separate sintering step“, inexpensive wire feedstock is significantly cheaper than the highly specific powders needed for DMLS for example. Sintering has been a notoriously difficult step to achieve for all of the binder jetting startups because the part shrinkage is not uniform, impossible to predict well and is different depending on the geometry, wall thickness and part size as well as the heating profile and process used. Xerox sidesteps this complexity here and also reduces cost because batches of parts do not have to go to debinding and then sintering after. All of these elements made them pull the trigger and afterward “keep investing.” Xerox is the right company to develop this technology further because, “we know jetting physics..and can ensure reliable and precise material placement.” They think that another key element is their AI-based software where “AI techniques” coupled with “physics-based modeling” will help them improve results and “make it easier to design for manufacturing.” Given their unique technology they can not use “an off the shelf slicer” to fill their 30 by 30 by 30cm build volume with aluminum. So they’re working on developing all of the needed software in parallel to developing the technology. At the moment they’re also working with “RIT Rochester on copper traces…improving the ‘image quality’..making the process faster..adding multiple nozzles or materials” and are aiming for a launch customer in 2020. They’re looking across many verticals, applications and materials at the moment for “commercial applications” and are very interested in “customers in automotive and aerospace” specifically for “light-weighting aluminum parts.”
It’s very appealing to us all to have jet another inkjet giant play in 3D printing. The Vader technology is new and I still can’t completely get my head around it. I’d be hugely interested if they can do gradient metal parts out of it on the fly, print parts with other metals mixed in for conductivity or print niche materials that others could not. If they can get their droplets all in order and find a niche then Xerox will have found its own unique path to the 3D printing market.
If you're looking to get an architectural rendering quote in the USA, our service provides a simple and efficient process to obtain the best pricing tailored to your project. Through our platform, you can easily submit your project details and receive a competitive quote from our team of experts. We offer high-quality 3D renderings for both interior and exterior designs, helping you bring your architectural visions to life with stunning precision. With our support, you can be confident in receiving professional services at affordable prices, without the hassle of dealing with multiple vendors.
Getting an accurate architectural rendering quote has never been easier. Through our portal, you’ll have direct access to a streamlined process where we guide you step by step, ensuring all your needs are met. Our 3D rendering experts work closely with you to ensure the final product matches your expectations, whether it’s for residential, commercial, or mixed-use developments. Trust our platform to provide you with the best possible rates and results, all with a quick turnaround time and exceptional customer support.