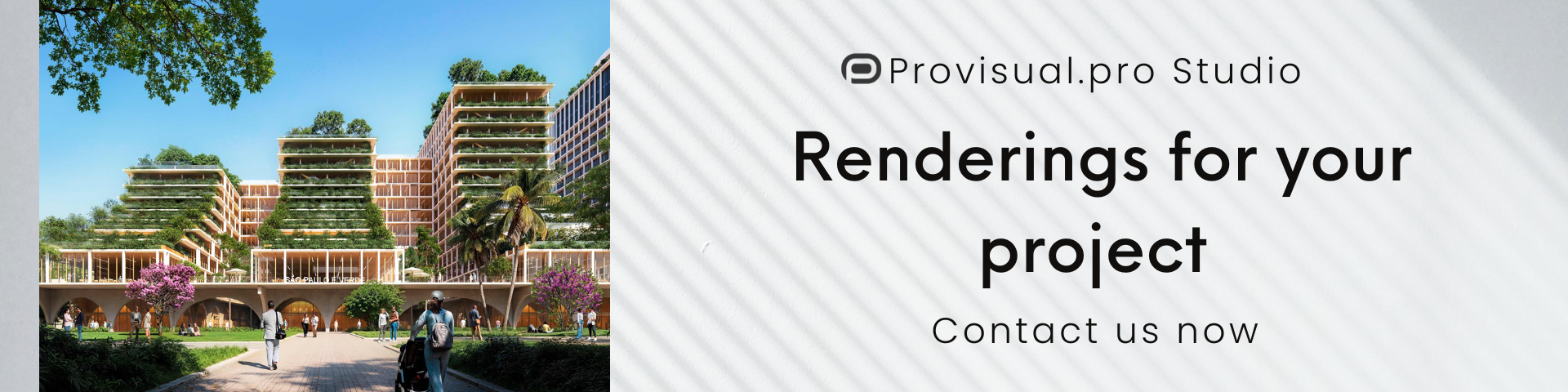
We’ve now seen how 3D printing can be used in bicycles, and in components. We’ve had a look at the most likely scenarios for 3D printing adoption and the preconditions for that adoption. But, what 3D printing technologies are to be used in bicycles? Below we outline the most relevant.
Short Fiber Carbon Fiber
We can use powder bed fusion and material extrusion to make short cut carbon fiber reinforced polymer parts. These are easy to make, also at scale and are more expensive than other polymer parts, but can exhibit high performance characteristics. Indeed such parts were created and shaped themselves by F1 guidelines. EOS, 3D Systems, Stratasys, Roboze, MiniFactory, INTAMSYS, AON3D and more can make such parts.
Medium-Format Polymer 3D Printing
Companies such as Juggerbot and Titan offer pellet 3D printers that can make accurate, reasonably cost-effective, polymer components that do not have an excellent surface finish but can be smoothed out by other processes. These parts can also use filled grades of polymers that can have many different properties.
Large-Scale Polymer 3D Printing
Cincinnati’s Big Area Additive Manufacturing process, as well as Large Scale Additive Manufacturing by Thermwood and MasterPrint from Ingersoll, can be used to print large polymer components and indeed many bike frames in one single build. It is advantageous to add short carbon and other fibers to these processes’ feedstocks. The cost performance is there, whereas the surface finish is not. Thermwood, Ingersoll and Cincinnati’s printers can also be used for large-scale molds for tooling and parts.
Continuous Carbon Fiber
There are a host of continuous carbon fiber technologies that could be used to make frames or components. Impossible Objects, Markforged, Orbital Composites, Arevo, Arris Composites, and others could play a part in directly replacing hand layup or other carbon fiber composites. Each of these technologies has a high degree of automation compared to manual labor, but have their own various limits as they each have their own approaches to carbon fiber part production.
Vat Polymerization and Casting
Stereolithography and digital light processing combined with lost wax and investment casting make tens of millions of parts in the jewelry and dental markets. For uncomplicated parts, these processes use a lot of manual labor in finishing the prints and final components, but they are cost-effective technologies that work at scale. For a lot of industrial uses, they are criminally overlooked and many people using direct metal 3D printing should probably be using this.
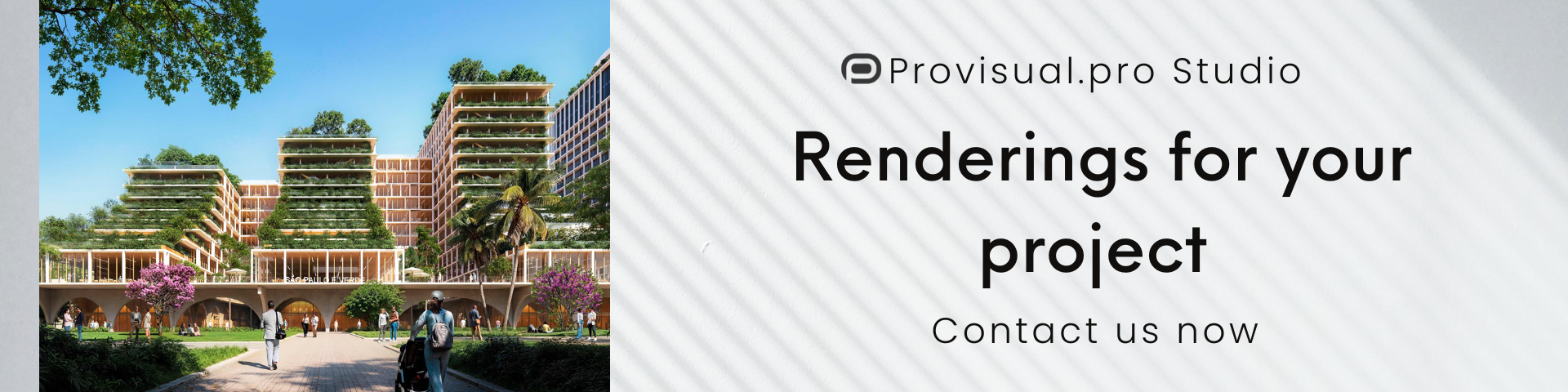
Powder Bed Fusion
Metal parts made with powder bed fusion are often from $50 to $300 per component, but they can use various steels, titanium, and aluminum. Part cost is high for cycling, but this would be the easiest mass customization metal technology to implement. Higher productivity machines and a downward trend in feedstock have made powder bed fusion more attractive of late.
Binder Jetting
Binder jetting can not quite make the intricate parts of powder bed fusion but it is much less expensive, producing at $10 to $100 per item. ExOne, Digital Metal, Desktop Metal, HP and GE are all trying to commercialize this technology for manufacturing at scale for automotive, but few bike firms are paying it enough attention. This can be used for a lot of cost-effective bike parts.
Directed Energy Deposition
Directed energy deposition (DED) is a host of technologies that spray or that use wire or powder to deposit metal onto a workpiece in some way. SPEE3D, Meltio, Sciaky, Optomec, MX3D, Formalloy and many others make very different technologies that could be used interchangeably to make large components and elements such as bike frames. Extensive post-processing would be required for these metal cheese whiz technologies, but they are very cost-effective owing to their low cost per machine hour and low cost per kilo of feedstock.
On the whole we can say that all of these technologies could play a part in 3D printing bicycles.
For the short carbon fiber and long carbon fiber polymer technologies, we could see them produce parts such as handlebars, seat components, other polymer components and, in some cases, structural elements. Surface finish and high cost will be limiting factors here. New design for additive manufacturing skills would have to be acquired by staff.
Some long carbon fiber technologies could be used for the manufacturing of entire frames. In fact, that is exactly what Arevo is doing. Labor as a component of cost would be lower, but currently the overall price would be higher than conventional manufacturing. It is also unclear now what the advantages would be, so more breakthrough design will have to be done to create bicycles that really take advantage of this.
Additionally medium- and large-format 3D printing could be used to make molds for carbon fiber or other tooling, as well as some frame-level components. Again surface finish and cost will be limiting factors. Strength and characteristics like young’s modulus over time for structural parts will also be potential barriers.
Vat polymerization combined with casting is ideal for shafts and shaft-like components, as well as small metal components like brake handles, shifters, handlebars, housings and, in some cases, parts such as stem elements. It is a multistep process and your design freedom is limited, but this is an extremely cheap technology to use if you do it in a country with low labor costs.
Powder bed fusion could be used for crankshafts, pedals, chainrings, hubs, some small frame components, seatposts, handle bar parts and entire groupsets. These items would be much more conventional than those made through current mass manufacturing processes. They could be designed to be significantly more lightweight, however. This could not only be used to make the bike lighter while customizing it to the rider, but also to change the characteristics of the bike. For example, we could change the center of gravity, take the weight off the front end, transfer weight to the bottom of the bike, etc. Design for powder bed fusion would be complicated and there would be a lot of post-processing, but these parts would be high performance.
DED and similar technologies could be used for frames. In this case, they could be leveraged to print the frame, stays, disks, and many other components in one integrated bicycle frame using far fewer components. In some cases, manufacturing like this may actually be cheaper than producing a carbon frame. Finishing processes would take up an extensive part of the costs for these processes, however.
Now, that we have somewhat of an idea of what 3D printing technologies are and can be used for what types of components, we’ll probably want to know, why should we want to use 3D printing at all?
If you're looking to get an architectural rendering quote in the USA, our service provides a simple and efficient process to obtain the best pricing tailored to your project. Through our platform, you can easily submit your project details and receive a competitive quote from our team of experts. We offer high-quality 3D renderings for both interior and exterior designs, helping you bring your architectural visions to life with stunning precision. With our support, you can be confident in receiving professional services at affordable prices, without the hassle of dealing with multiple vendors.
Getting an accurate architectural rendering quote has never been easier. Through our portal, you’ll have direct access to a streamlined process where we guide you step by step, ensuring all your needs are met. Our 3D rendering experts work closely with you to ensure the final product matches your expectations, whether it’s for residential, commercial, or mixed-use developments. Trust our platform to provide you with the best possible rates and results, all with a quick turnaround time and exceptional customer support.