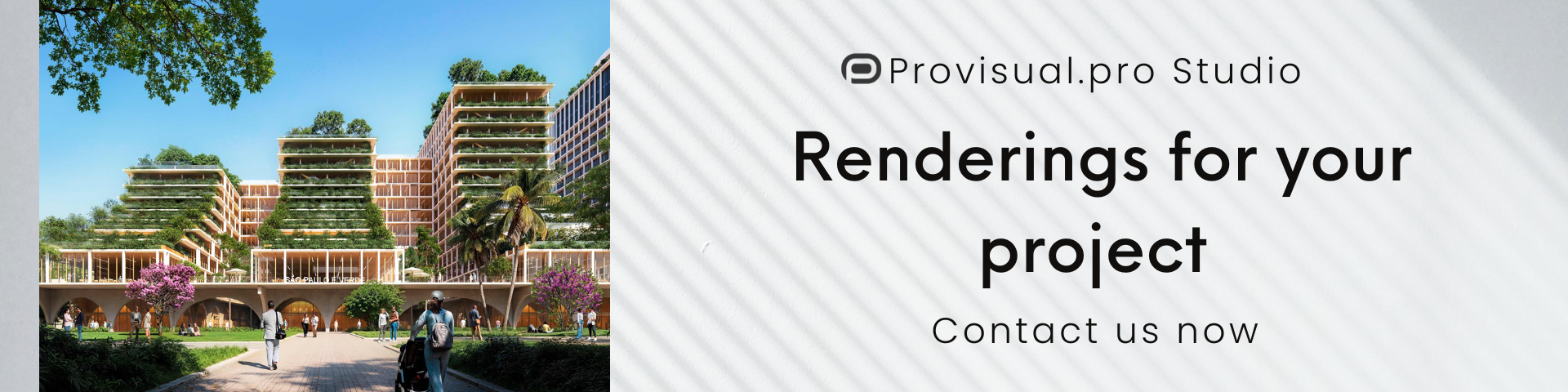
Star Wars toys were, to put it mildly, a big part of my childhood. My neighbor and best friend at the time and I took our Star Wars toys very seriously and would strategically plan which of our parents would be willing to get us which toys so we had as many Star Wars toys to play with as possible. My mother didn’t mind buying me action figures, but she hated buying me the playsets because she felt that you only ever really needed one playset, which is totally ridiculous for obvious reasons. It took almost six months of pleading, lots of chores and some quality butt-kissing to convince my mom to buy me an AT-AT walker but on my ninth birthday it was finally mine. And just like with all of my toys I enjoyed the heck out of it, but I’d be lying if I said that it didn’t cross my mind how awesome it would be if the AT-AT actually walked by itself.
A mechanical engineering student from the University of Michigan uploaded a project to Thingiverse that would have made my nine-year-old self’s head explode. Dan Olsen designed and 3D printed a Motorized Star Wars AT-AT that is just as big as the toy version that I had as a kid. The 3D printed version may not have the detail that the original toy had, but it is close enough that imaging it walking by itself among my figures would have made nine-year-old me quite happy. While nowadays there are RC versions of the AT-AT, I think that this version is cooler because it walks all on its own thanks to the internal 3D printed gears that only need to be connected to a single motor.
Other than the motor, the switch and the 9V battery clip, everything in Olsen’s model is entirely 3D printed. The design includes 69 individual parts and components that require a little over 750 grams of filament to complete — although Olsen is quick to point out that most of the parts are small components and don’t take an incredible amount of time to produce. He estimates that he only spent about four days printing for everything, and that was for multiple sets. Inside the AT-AT is a collection of gears and motor parts that were designed to give it the same herky jerky movements from the movie, and all four legs are powered by the same 90 rpm motor.
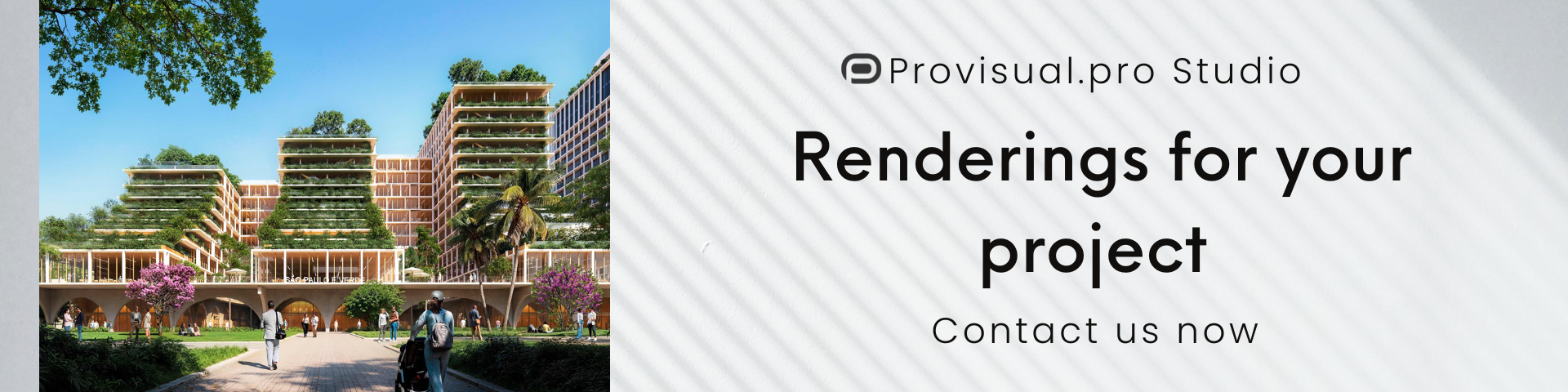
“Well I realized that the system to move an individual leg was going to be more or less the same if I used a motor for each leg or if I just connected them all to one motor. The walk cycle I guess is supposed to be one leg at a time so that makes it fairly straightforward to cycle through the four legs. I watch the scene in the movie and broke the leg movement down to an action of lifting the leg and rotating it at the joint. I had a little experience with the type of gear that lifts the leg. I used nearly the identical design in this model . the gear that rotates the leg at the joint took a lot of time to get right. It has to go from a slow speed to a fast speed every time the leg strides. Like this , just getting the right ratios was difficult,” Olsen explained.
Here is some video of the AT-AT walking and of the gears hidden inside of it:
Olsen’s AT-AT was designed in Solidworks and 3D printed on his home-built MendelMax 2 with a .4mm nozzle. The design won’t require any rafting, however some of the parts will need supports to print properly. Most of the parts were printed at 0.2 mm resolution, while the main body parts and head pieces were printed at 0.3mm. Everything was printed with a 10% infill. Some of the parts are quite large, and because of the gears it isn’t possible to scale down the model, so there may be some adjustments to make if the AT-AT is being printed on a printer with a smaller build envelope. The largest component is the main body part which is about 205mm (8 inches) long and 110mm (4.3 inches) wide. Olsen has included a version of the body that was cut into two pieces and is notched so they can easily be joined.
In order to make sure that the gears all worked correctly, and to prevent any deformations and warping, Olsen included a brim for any of the gear parts touching the build plate. Naturally this means that there is going to be some post processing work involved in building the AT-AT, but it also means that the gears will work better. Depending on the printer being used to print any parts the gears may also need to be filed in between the teeth a bit just to smooth them out. Olsen included a very detailed set of assembly instructions here. And of course if you want to build your own walking AT-AT then you can download the Thing files here. Discuss this story in the 3D Printed AT-AT forum thread on 3DPB.com.
If you're looking to get an architectural rendering quote in the USA, our service provides a simple and efficient process to obtain the best pricing tailored to your project. Through our platform, you can easily submit your project details and receive a competitive quote from our team of experts. We offer high-quality 3D renderings for both interior and exterior designs, helping you bring your architectural visions to life with stunning precision. With our support, you can be confident in receiving professional services at affordable prices, without the hassle of dealing with multiple vendors.
Getting an accurate architectural rendering quote has never been easier. Through our portal, you’ll have direct access to a streamlined process where we guide you step by step, ensuring all your needs are met. Our 3D rendering experts work closely with you to ensure the final product matches your expectations, whether it’s for residential, commercial, or mixed-use developments. Trust our platform to provide you with the best possible rates and results, all with a quick turnaround time and exceptional customer support.