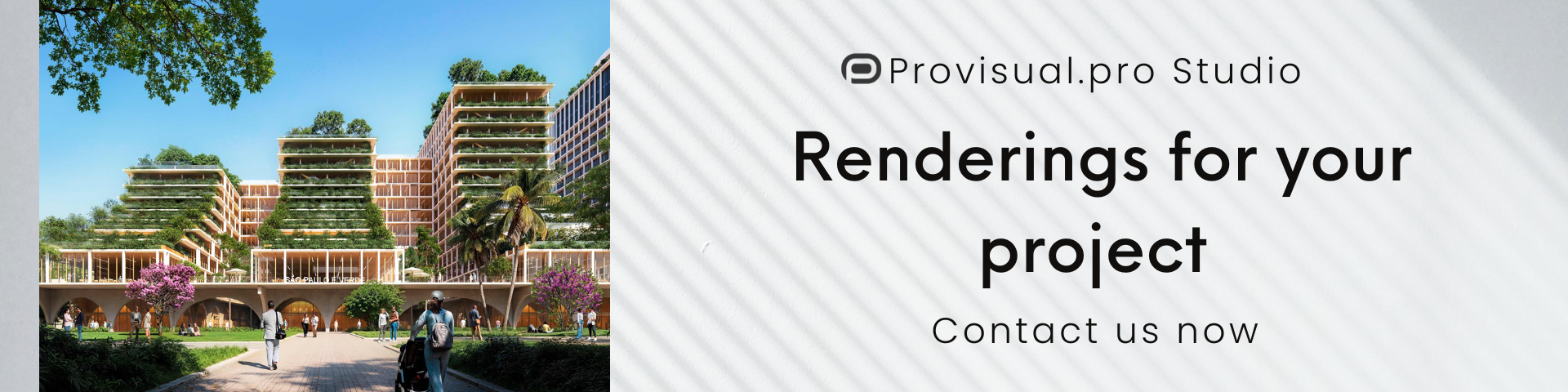
Scientists from China’s Shenzhen University have explored a new technique using additive manufacturing to optimize the “heart” of a nuclear fusion reactor, its tritium production unit.
In research, military and industrial applications, the commonly used fuel elements for nuclear fusion reactions are deuterium and tritium. Deuterium is easily available on Earth, obtainable from sources such as seawater. Tritium, on the other hand, is extremely hard to find naturally on the planet, and can only be produced at a commercial scale by a continuous catalytic reaction between helium and lithium ceramics (such as lithium titanate and lithium orthosilicate). “Breeding blankets” are made of these lithium ceramics, in pebble form, to produce tritium in enough quantities for the nuclear reactor to function. The tritium production unit is this breeder blanket mechanism where breeder materials, lithium orthosilicate and helium, react to form tritium. The lithium orthosilicate is made in the form of microspheres (about 1 mm in diameter) which are stacked to form a bed structure, through which helium can be injected.
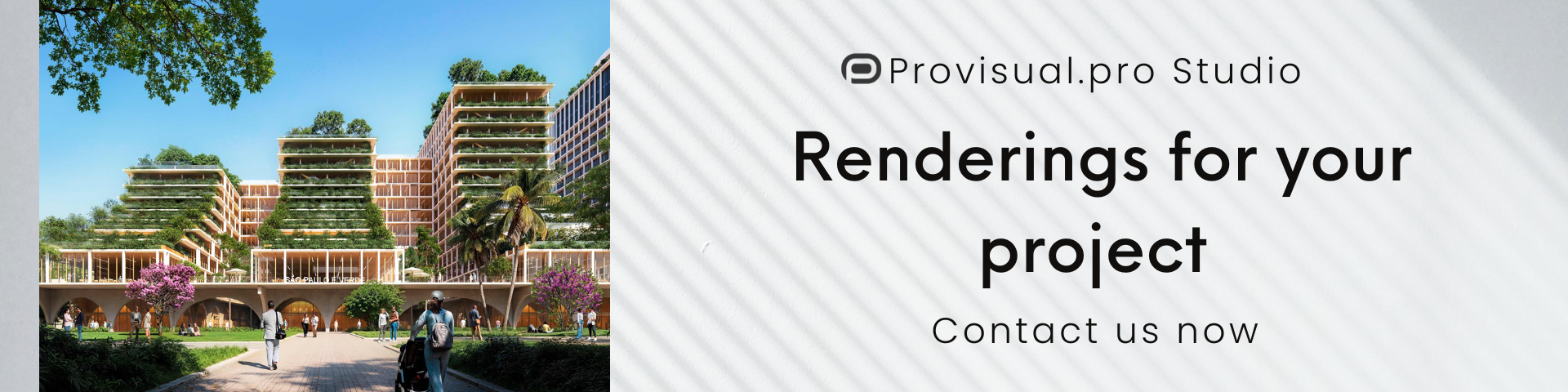
The traditional approach to manufacturing the bed structure has limitations in the filling rate which cannot be freely regulated. Stress concentrations caused by the packing of the microspheres can also cause deformation or cracking of the tritium production unit, threatening the uniform stability of the bed and constraining the structure. Optimizing and ensuring the stability and structure of tritium production units is one of the key challenges faced by scientists in building commercial nuclear fusion reactors.
This is where Professor Chen Zhangwei of the Additive Manufacturing Institute of Shenzen University explored 3D printing the lithium orthosilicate breeder blanket structures. The researchers used DLP-based ceramic 3D printing, with a 405 nanometer ultraviolet light for curing, to produce a porous structure with fewer cracking defects and higher accuracy than if it was powder sintered or melted.
According to the team, the 3D printed tritium production unit has an integrated, defect-free structure that does away with reliability issues caused by limited filling rates and stress concentrations, improving mechanical properties by a factor of two and increasing the specific surface area of lithium orthosilicate, over the traditional microsphere structure. In addition, the 3D printed structure, with tailorable packing fraction for breeder structure requirements, has greater efficiency than a traditional microsphere structure. Duty cycles for the 3D printed structure can be adjusted between 60-90%, while the traditional structure has a duty cycle of 65%.
Such applications prove and expand the scope of additive manufacturing in research and production of advanced nuclear energy systems, particularly in manufacturing, integrating sensors and controls, optimizing complex components for better performance, and even in recycling nuclear fuel. In 2018, researchers at the Chinese Academy of Sciences successfully trialled production of the cladding wall, a key component of nuclear fusion reactors, using SLM and anti-neuron irradiated steel (CLAM steel) as raw material. Just this May, Oak Ridge National Laboratory used Directed Energy Deposition (DED) and stainless steel to design a prototype of a 3D printed nuclear reactor core. Further, the world’s largest fusion reactor, ITER, an ambitious global project involving 35 countries set on proving commercial production of fusion-based electricity, has just entered assembly phase and is set to be completed in 2025 in Southern France.
If you're looking to get an architectural rendering quote in the USA, our service provides a simple and efficient process to obtain the best pricing tailored to your project. Through our platform, you can easily submit your project details and receive a competitive quote from our team of experts. We offer high-quality 3D renderings for both interior and exterior designs, helping you bring your architectural visions to life with stunning precision. With our support, you can be confident in receiving professional services at affordable prices, without the hassle of dealing with multiple vendors.
Getting an accurate architectural rendering quote has never been easier. Through our portal, you’ll have direct access to a streamlined process where we guide you step by step, ensuring all your needs are met. Our 3D rendering experts work closely with you to ensure the final product matches your expectations, whether it’s for residential, commercial, or mixed-use developments. Trust our platform to provide you with the best possible rates and results, all with a quick turnaround time and exceptional customer support.