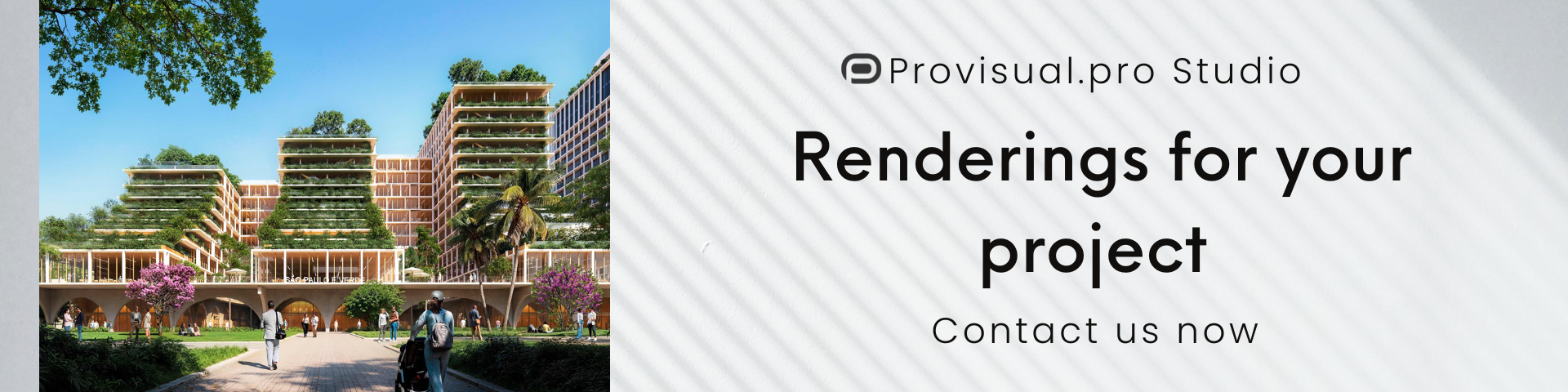
Despite the wide range of prosthetics available today, those with partial hand loss are often left out in the cold—and with a disability that often proves to be extremely challenging due to a significant loss of dexterity. Researchers from University of Colorado and Rice University aim to change that with a new design for a finger prosthesis that is fully articulated, featuring a self-contained actuator. The project and subsequent testing are detailed in their recently published paper, ‘Design and evaluation of a distally actuated powered finger prosthesis with self-contained transmission for individuals with partial hand loss.’
Using direct laser metal sintering (DMLS), the research team created a gear transmission for the medial phalanx portion of the finger. The transmission then connects with the DC motor, allowing torque transmission across the PIP joint. This new design features an automated device that is like the index finger size of a female in the 25-50th percentile. While this is an average size, in the future sizing may be possible for other amputees. For proper balance and ‘perception of the prosthesis as an external load worn on the residual limb,’ the scientists designed it with a weight like a human finger.
“The finger phalanges and underactuation mechanism form a six-bar linkage and is essentially a superposition of two four-bar linkages commonly used to underactuate two-phalanx commercial and research devices,” state the researchers. “The linkage system couples the motion of each IP joint to provide a flexion trajectory suitable for a variety of grasps used in ADL.
Testing was centered around evaluating force and flexion of the fingertips, using an Escon 24/2 controller from Maxon Motors powered at 12 V, and a Futek LSB200 load cell powered at 24 V for connecting with the fingertip at varying angles. The researchers also used a Quanser Q8-USB data acquisition board using MATLAB/Simulink to collect the following:
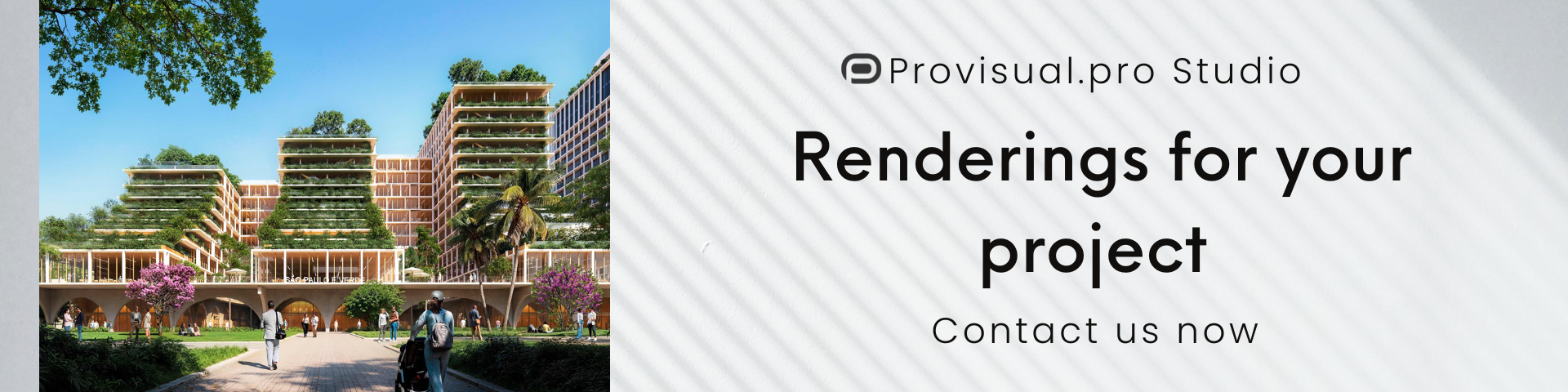
- Collected load cell force
- Motor current draw
- Voltage
In evaluating force of the prosthetic finger, the researchers position the load cell within contact of the fingertip, while the controller powered the motor—driving the finger to the load cell. After that the researchers set up the following steps:
- The motor was powered for .5 seconds after detecting the impulse load.
- The holding force was recorded.
- The load cell was moved to contact the fingertip to measure the flexion speed.
- Flexion speed was determined by ‘dividing the time the finger took to contact the load cell from its fully extended position by the angular displacement of the finger.’
The researchers repeated the trials 15 times. As they began evaluating individual gear stages, the team realized further examination would be needed to assess contributions of the face gear pair to transmission efficiency. Mechanics of the fingers will require more validation too, along with further fatigue testing.
“Ongoing work on the powered finger has resulted in a more compact and higher reduction power transmission and future work will include a closer evaluation of the transmission efficiencies to determine the benefit of using face gears and the changes made to the structure of planetary gear stages,” concluded the researchers. “Alternative gearings that increase the overall reduction of the transmission while decreasing the number of gear stages necessary is of interest, in addition to a more thorough examination of the gear polishing process.
“Work will also include refinements to the residual limb attachment that better accommodates individuals with amputations distal to the MCP, as well as improvements to the robustness and anatomical motion of the kinematic link bar system. Upcoming iterations of the finger will also include improvements to its performance in opposition and safety mechanisms to protect the components in extreme or unexpected loading cases.”
3D printing has earned an honorable niche in the world of prosthetics, undeniably changing the lives of many, from prosthetics that help veterans, to amphibious limbs, to prosthetic breasts for mastectomy patients. What do you think of this news? Let us know your thoughts; join the discussion of this and other 3D printing topics at 3DPrintBoard.com.
[Source / Images: Design and evaluation of a distally actuated powered finger prosthesis with self-contained transmission for individuals with partial hand loss]
If you're looking to get an architectural rendering quote in the USA, our service provides a simple and efficient process to obtain the best pricing tailored to your project. Through our platform, you can easily submit your project details and receive a competitive quote from our team of experts. We offer high-quality 3D renderings for both interior and exterior designs, helping you bring your architectural visions to life with stunning precision. With our support, you can be confident in receiving professional services at affordable prices, without the hassle of dealing with multiple vendors.
Getting an accurate architectural rendering quote has never been easier. Through our portal, you’ll have direct access to a streamlined process where we guide you step by step, ensuring all your needs are met. Our 3D rendering experts work closely with you to ensure the final product matches your expectations, whether it’s for residential, commercial, or mixed-use developments. Trust our platform to provide you with the best possible rates and results, all with a quick turnaround time and exceptional customer support.