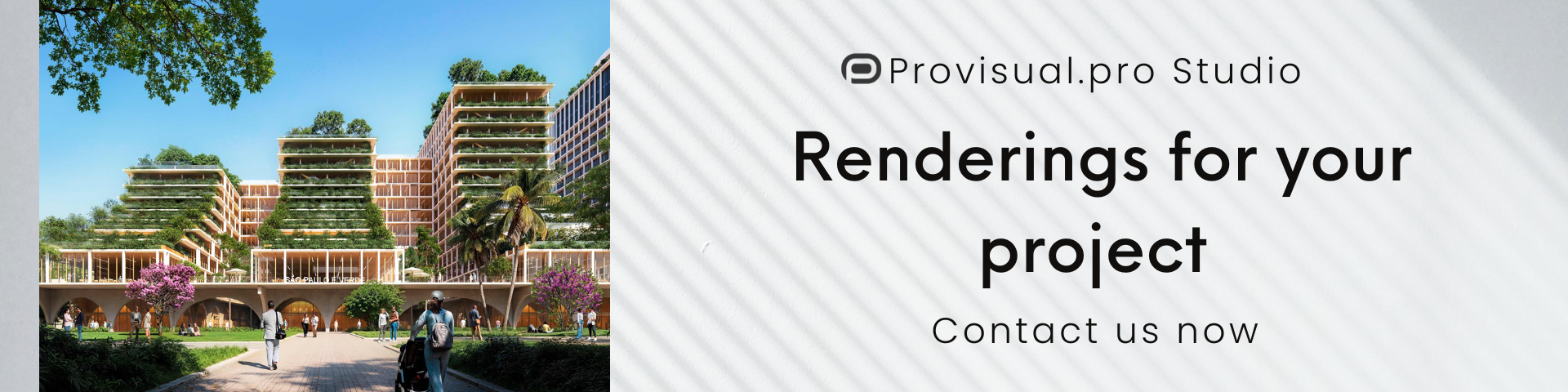
Self-examination is a component of practice in any area that has begun to coalesce into a field in its own right. The development of an academic interest in the history and progress of additive manufacturing is the hallmark of a budding field that moves beyond mere technique. Faculty from Engineering and Information Sciences part of the alliterative School of Mechanical, Materials, and Mechatronic Engineering at the University of Wollongong in New South Wales, Australia have recently published just such a reflexive piece in the Journal of Advanced Manufacturing Technology.
In their article, the authors proposed to review wire-feed advanced manufacturing technologies with an eye to identify the current challenges of the technique as well as to discuss possible directions for future research. One of the reasons for their focus was the paucity of research on the wire-feed process side of additive manufacturing, the most attention having been paid to its more glamorous cousin powder-feed/-bed additive manufacturing. As is obvious from the name, in wire-feed the manufacturing supply material is metal wire rather than metal powder.
They began by making an argument for the strengths of wire-feed additive manufacturing because the low deposition rates of powder-feed techniques make them less than ideal for the fabrication of mid- to large-sized components. In addition, the efficiency of material usage (approaching 100%) in wire-feed makes it a more environmentally friendly process for manufacturing, as well as creating a significant reduction in input material expenses. For these reasons, they argue, a more in-depth examination of wire-feed techniques is warranted.
Wire-feed additive manufacturing is not without problems. While being a very promising technology for the production of moderately complex, large components for industries such as aerospace, automotive, and rapid tooling, there are some limitations that must be addressed. Currently, wire-feed additive manufacturing produces parts with a poor surface finish and cannot create with as high of a degree of accuracy because of the “stair stepping” effect. The first step toward addressing the issues that wire-feed additive manufacturing faces is to ensure a comprehensive review of identified challenges.
The paper written by the faculty at Wollongong is divided into four sections. In the first, they introduce the need for a comprehensive study. In the second section they provide a detailed description of current wire-feed processes, followed by a third section discussing the challenges and current scholarship in the area. Finally, in the final section they look to the future and point out possible directions for continuing investigation.
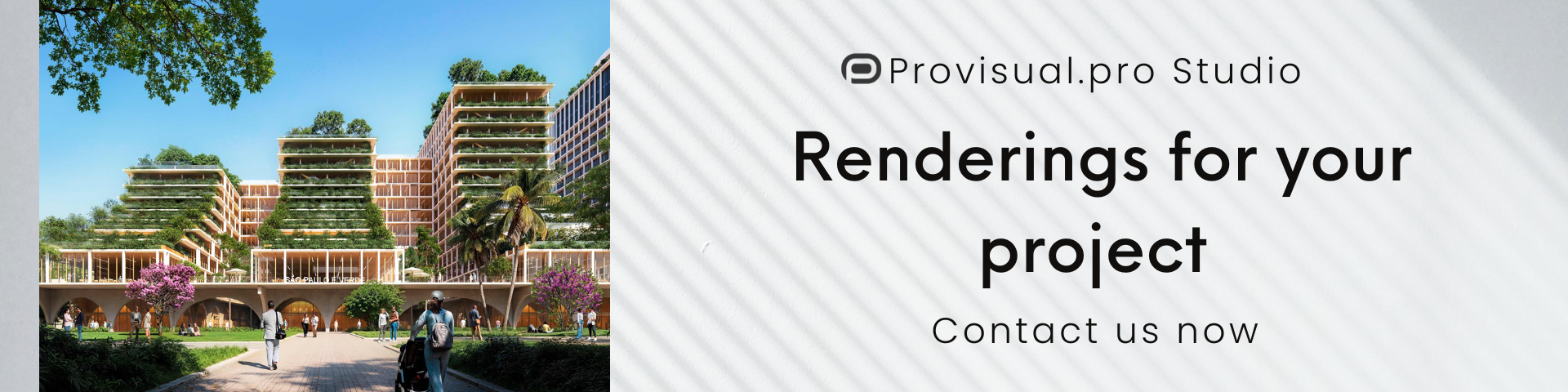
Wire-feed additive manufacturing is divided into three groups depending on whether it uses a laser, arc welding, or electron beam as the energy source. Each type has its strengths and weaknesses and the authors provide an in-depth analysis of each, weighing them against each other and in terms of efficiency, energy, and material usage. One of the most interesting is a technique called Electron Beam Freeform fabrication (EBF) patented by NASA to build complex, near-net-shapes. This process uses significantly less material and requires a relatively minimal amount of finish machining in comparison to more traditional methods of manufacture.
The EBF heat source technique works by introducing the feedstock (metal wire) into a molten pool in a high vacuum environment using a focused electron beam. This process allows for bulk metal deposition rates of over 2500 cm3 / h and for a much finer level of detail even at lower deposition rates. The size of the features that can be obtained with this process is determined by the diameter of the wire feedstock with finer wires yielding finer details.
Each of the production techniques covered carries with it a set of benefits and challenges. Much of the current research in the area is dedicated to addressing the recognized weaknesses of wire-feed additive manufacturing. Especially important to the potential for the technology is increased ability to control the residual stresses and distortions in large-scale wire-feed additive manufacturing when undertaken using arc welding as a heat source.
The researchers identify as being of particular significance for future development of wire-feed additive manufacturing issues of material quality, improvements in design for additive manufacturing, increased capacity for monitoring and process control, and the introduction of more effective milling strategies. The authors briefly address each of these areas and the ways in which they envision future contributions made by research to the improvement of the functionality of wire-feed additive manufacturing.
This type of review of literature and state of the technology article is often only of interest to a specific group of scholars in a field. However, given the nature of additive manufacturing and the accessibility of the information as presented by the authors, despite its appearance in an academic journal, makes it a piece of interest to anyone seeking to bring themselves up to speed in this promising area of wire-feed additive manufacturing.
Let us know what you think of this research in the Wire-Feed Additive Manufacturing forum thread over at 3DPB.com.
If you're looking to get an architectural rendering quote in the USA, our service provides a simple and efficient process to obtain the best pricing tailored to your project. Through our platform, you can easily submit your project details and receive a competitive quote from our team of experts. We offer high-quality 3D renderings for both interior and exterior designs, helping you bring your architectural visions to life with stunning precision. With our support, you can be confident in receiving professional services at affordable prices, without the hassle of dealing with multiple vendors.
Getting an accurate architectural rendering quote has never been easier. Through our portal, you’ll have direct access to a streamlined process where we guide you step by step, ensuring all your needs are met. Our 3D rendering experts work closely with you to ensure the final product matches your expectations, whether it’s for residential, commercial, or mixed-use developments. Trust our platform to provide you with the best possible rates and results, all with a quick turnaround time and exceptional customer support.